A Tailored Solution Ensures Dairy Plant Safety and Productivity
Sign Up for Maintenance Tips
Posted on May 25, 2022 10:53:00 AM by AGC Heat Transfer | 2 min. read
Penny Vander Velden, former Plant Manager and Director of Operations at a Wisconsin dairy cooperative, received best-in-class service when reaching out to AGC Heat Transfer for a unique safety concern at their plant. The situation called for specialized modifications to conform with their limited space while maintaining normal production output. Our goal was to deliver an exceptional customer experience that would result in a big success for the facility.
The Challenge of Ensuring Safety and Productivity Within a Limited Space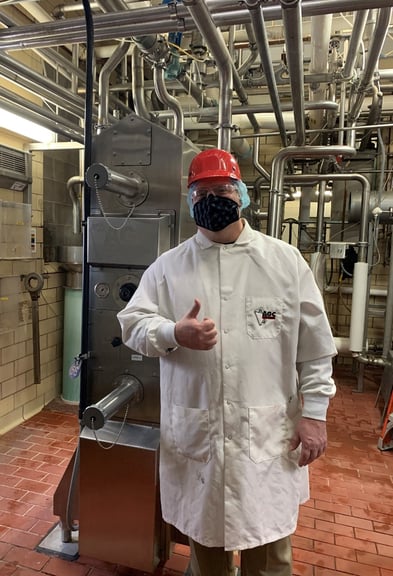
Not long ago, a new heat exchanger unit was required at one of the dairy cooperative's facilities in an area that was run by a single person. This sole employee wore many hats to keep the facility running. As a result, it was critical that the new exchanger be quick and easy to operate due to the facility's frequent inspections.
The design of this area of the facility was also unique, in that it was narrow and generally smaller than the rest of the plant, demanding the need for the perfect fit.
Unlike typical smaller-sized heat exchanger units, the ideal unit would need to include hydraulics. This created a problem for this dairy cooperative, considering that most hydraulic heat exchanger units are not customized to fit in such a small footprint.
Why the Customer Chose AGC Heat Transfer
For years, AGC Heat Transfer has provided trusted service and support across all of this dairy cooperative's facilities. And AGC has consistently maintained a good relationship with them by offering reliable service, conducting regular plate checks, overnighting spare plates, and even sending service technicians at the last minute when necessary. To put it simply, when our customers call, we answer on the first ring.
How AGC Responded
Our team of engineers and designers immediately began brainstorming safe and innovative ways to address the problem. We collaborated with Penny to fine-tune solutions without sacrificing safety or production capability. Careful consideration was required to tailor a heat transfer unit to fit the tight space. And knowing that the heat exchanger would largely be operated by a single individual, the hydraulic design removed the need for manual motion in order to open and close the exchanger, making it easier and safer for the employee to open the machine at the necessary frequency.
AGC made it happen and in December 2020, the new unit was successfully installed.
The Result
As a result, the dairy cooperative was once again impressed by our ability to provide a customized solution to their problem. Without sacrificing either of their top two priorities, AGC was able to deliver a win-win outcome that ensured maximum production capability at the highest level of safety. It’s another example of how AGC Heat Transfer goes above and beyond to serve the needs of our partners as leaders in the industry.
Put Our Team to the Test
If your business is experiencing unique challenges, contact our team to see what type of innovative solutions we can provide. We don’t shy away from a challenge — we embrace it!
Topics: Maintenance | Service | AGC Way | Testimonials